Strain Gauge
Strain gauges are sophisticated sensory devices used to measure mechanical strain in materials. Their importance lies in their ability to provide accurate and reliable measurements, allowing for a deeper understanding of material behavior and structural integrity.
The historical evolution of strain gauges dates back to the late 19th century when Lord Kelvin developed the concept of electrical resistance. Their evolution has been marked by advancements in technology, leading to the development of various types of strain gauges.
Strain measurements play a crucial role in numerous fields, including engineering, research, and industrial sectors. They provide valuable insights into the behavior of materials under different conditions, aiding in designing and optimizing structures and products.
Strain gauges are designed to detect changes in the length of an object or material when subjected to an external force or load. These changes result in deformations known as strains. By measuring these strains, engineers and researchers can gather essential data about the mechanical properties and performance of materials.
The historical journey of strain gauges is closely tied to the evolution of electrical resistance theory. Lord Kelvin's pioneering work in the late 19th century laid the foundation for understanding how the resistance of a conductor changes when it undergoes mechanical deformation. This concept formed the basis for the development of strain gauges.
Over the years, technological advancements have led to the creation of various types of strain gauges, each catering to specific measurement requirements. These gauges are constructed using thin wires, foils, or semiconductor materials. As the material experiences strain, its electrical resistance changes proportionally, which can be measured and correlated to the applied force or stress.
Strain gauges have become indispensable tools in modern engineering and scientific research. They are extensively used in fields such as aerospace, civil engineering, automotive, and biomechanics. In aerospace applications, strain gauges monitor the structural health of aircraft components, ensuring safety and reliability. Civil engineers employ strain measurements to assess the integrity of bridges, dams, and buildings under various loads and environmental conditions.
The automotive industry relies on strain gauges to evaluate the performance and durability of vehicle components. In biomechanics, these devices aid in studying human movement and the interaction between muscles, bones, and external forces.
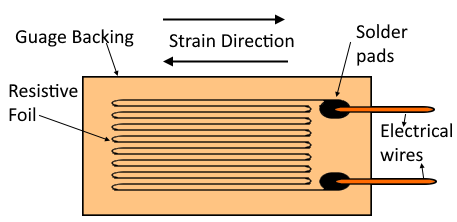
Understanding Strain Measurements
- Concept of Mechanical Strain in Materials - Mechanical strain refers to the deformation experienced by a material when subjected to external forces. - It is measured as the fractional change in the material's length, area, or volume.
- Importance of Accurate Strain Measurements - Accurate strain measurements enable engineers and researchers to understand how materials respond to external loads. - This understanding is vital for designing safe and efficient structures, predicting failures, and optimizing performance.
- Different Types of Strain: Tensile, Compressive, Shear, and Bending - Tensile strain occurs when a material is stretched, while compressive strain occurs when it is squeezed. - Shear strain describes the deformation resulting from forces applied parallel to a material's surface. - Bending strain refers to the deformation that occurs when a material is subjected to a combination of tensile and compressive forces.
Basics of Strain Gauge Technology
- Construction and Composition of Strain Gauges - Strain gauges consist of a thin metallic foil or semiconductor material attached to a flexible backing. - The composition is carefully selected to exhibit the desired electrical resistance changes when strained.
- Principle of Piezoresistance: Unveiling the Working Mechanism - The working mechanism of a strain gauge is based on the principle of piezoresistance. - Piezoresistive materials exhibit a change in electrical resistance when subjected to strain.
- Factors Influencing the Performance of Strain Gauges - The performance of strain gauges is influenced by factors such as temperature, humidity, and adhesive compatibility. - Calibration and installation techniques also play a vital role in ensuring accurate and reliable measurements.
Types of Strain Gauges
- Metal Foil Strain Gauges: Most Common and Versatile Type - Metal foil strain gauges are widely used due to their excellent durability, flexibility, and cost-effectiveness. - They are suitable for a broad range of applications, including automotive, aerospace, and material testing.
- Semiconductor Strain Gauges: Enhancing Sensitivity and Precision - Semiconductor strain gauges offer higher levels of sensitivity and precision compared to metal foil gauges. - They are commonly used in applications that require extremely accurate measurements, such as atomic force microscopy.
- Thin-Film Strain Gauges: High Stability and Resistance to Environmental Effects - Thin-film strain gauges exhibit enhanced stability and resistance to environmental influences, such as temperature variations and humidity. - They are often used in applications where long-term measurements or exposure to extreme conditions are required.
- Advanced Optical Strain Gauges: Utilizing Optical Interferometry - Advanced optical strain gauges employ optical interferometry principles to measure strain. - They offer exceptional precision and are commonly used in research and specialized applications.
Installation and Mounting Techniques
- Proper Pre-Installation Considerations - Before installing strain gauges, it is imperative to consider factors such as material properties, surface conditions, and strain gauge orientation. - Proper planning and preparation ensure accurate and reliable measurements.
- Surface Preparation Methods - The surface preparation of the material is vital for achieving optimal performance from strain gauges. - It typically involves cleaning, roughening, and applying a suitable primer or adhesive to maximize adhesion.
- Selecting Suitable Adhesives and Protective Coatings - The choice of adhesive and protective coating depends on the material being tested and the environmental conditions involved. - The selected materials should ensure proper bonding, electrical insulation, and protection against moisture and contaminants.
- Mounting Techniques for Different Applications: Static vs. Dynamic Measurements - Static measurements require strain gauges to be securely attached to the material. - Dynamic measurements involve mounting techniques that minimize the effects of vibration and strain rate variations.
Calibration and Measurement Accuracy
- Importance of Calibration in Ensuring Accuracy - Calibration is essential for achieving accurate and reliable strain measurements. - It involves establishing a known relationship between the electrical output of the strain gauge and the applied strain.
- Calibration Techniques for Strain Gauges: Dummy and Shunt Calibration - Dummy calibration involves applying a known strain to the structure to validate the measurements obtained. - Shunt calibration involves the application of a known resistance in parallel with the strain gauge to verify its accuracy.
- Evaluating Measurement Uncertainty and Error Sources - Measurement uncertainty should be carefully evaluated to determine the level of confidence in the obtained strain measurements. - Sources of error, such as temperature variations, electrical noise, and strain gauge aging, should be identified and minimized.
Strain Gauges in Structural Health Monitoring
- Assessing Structural Integrity and Preventing Failures - Strain gauges play a critical role in the monitoring and assessment of structural integrity. - They help identify potential weaknesses, predict failures, and prevent catastrophic incidents.
- Real-Time Monitoring of Bridges, Dams, and Buildings - Strain gauges installed on bridges, dams, and buildings provide real-time data on structural behavior, ensuring their safe operation. - Continuous monitoring allows for early detection of any abnormalities, enabling timely maintenance and repairs.
- Integration of Strain Gauges with Wireless Sensor Networks - Strain gauges can be integrated into wireless sensor networks, providing easy access to data and simplifying monitoring systems. - This integration enhances data collection, analysis, and decision-making processes.
Industrial Applications of Strain Gauges
- Automotive Industry: Enhancing Vehicle Safety and Performance - Strain gauges are extensively used in the automotive industry to measure stresses and strains in components and structures. - They aid in improving vehicle safety, optimizing performance, and ensuring compliance with safety standards.
- Aerospace Industry: Ensuring Structural Integrity of Aircraft - Strain gauges are crucial in the aerospace industry for monitoring the structural health of aircraft. - They provide vital information on stress distribution, fatigue, and load-bearing capacities, ensuring safe and reliable flight operations.
- Energy Sector: Monitoring Stress in Wind Turbines and Power Plants - In the energy sector, strain gauges are employed to monitor stress levels in critical infrastructure such as wind turbines and power plants. - Accurate strain measurements help optimize maintenance schedules, prevent downtime, and ensure the long-term reliability of these assets.
Strain Gauges in Material Testing and Research
- Measuring Material Properties and Behavior - Strain gauges enable researchers to measure and analyze the behavior of materials under various conditions. - This information is valuable for understanding material properties, exploring new applications, and enhancing product development.
- Investigating the Strength and Durability of Various Structures - Strain gauges play a crucial role in investigating the strength, durability, and failure mechanisms of structures. - They help engineers design resilient structures and ensure they meet safety requirements.
- Applications in Biomechanics and Medical Research - Strain gauges find applications in biomechanics and medical research, aiding in the study of human movement and physiological response. - They contribute to the development of medical devices, orthopedics, and rehabilitation techniques.
Strain Gauges in Robotics and Automation
- Optimizing Efficiency and Performance in Robotics - Strain gauges are employed in robotics to monitor the forces and strains experienced by robotic components. - This information enables optimization of performance, control, and efficiency in robotics applications.
- Implementing Feedback Control Systems - Strain gauges play a pivotal role in feedback control systems, enabling real-time adjustments and corrections. - They contribute to precision, stability, and safety in various industrial and automation processes.
- Enhancing Precision in Industrial Automation - Strain gauges are integrated into industrial automation systems to measure and control crucial parameters. - Their ability to provide precise strain measurements enables accurate process control and enhances overall system performance.
Emerging Trends and Future Prospects
- Miniaturization of Strain Gauges for Microscopic Applications - The miniaturization of strain gauges opens up possibilities for microscopic applications in fields like microelectronics and nanoengineering. - These highly sensitive sensors contribute to advancements in miniaturized devices and systems.
- Integration of Strain Gauges with IoT and Data Analytics - Strain gauges integrated with the Internet of Things (IoT) facilitates the collection and analysis of strain data on a large scale. - This integration enables proactive maintenance decisions, predictive analytics, and optimization of processes.
- Advancements in Wireless Strain Gauge Technology - Wireless strain gauge technology continues to advance, allowing for more reliable and efficient data transmission without physical connections. - This trend contributes to the development of wireless monitoring systems and expands the possibilities for remote and distributed applications.
Challenges and Limitations of Strain Gauges
- Sensitivity to Temperature Variations - Strain gauges are sensitive to temperature changes, which can introduce inaccuracies in the measurements. - Proper temperature compensation techniques are necessary for maintaining measurement accuracy.
- Strain Gauge Fatigue and Lifespan Considerations - Strain gauges experience cyclic loading, leading to fatigue and reduced lifespan. - Monitoring fatigue and implementing appropriate maintenance practices is crucial for reliable and continuous operation.
- Issues Related to Humidity and Environmental Influences - Humidity and environmental factors such as moisture and contaminants can affect strain gauge performance. - Proper sealing and protection measures should be implemented to mitigate these influences.
Benefits and Advantages of Strain Gauges
- Non-Disruptive Testing and Monitoring in Real Time - Strain gauges offer non-disruptive testing and monitoring capabilities, allowing measurements to be taken without disturbing the material or structure under investigation. - Real-time data acquisition ensures prompt responses to changes and deviations.
- High Precision and Accuracy in Strain Measurement - Strain gauges provide highly precise and accurate strain measurements, enabling engineers and researchers to make informed decisions and predictions. - The reliability of the measurements contributes to efficient design, optimization, and maintenance processes.
- Cost-Effectiveness and Versatility in Various Applications - Strain gauges offer a cost-effective solution for a wide range of applications. - Their versatility allows them to be used in different industries, addressing diverse measurement needs.
Summary and Conclusion
In conclusion, strain gauges play a vital role in measuring mechanical strain and understanding material behavior. They have evolved over time, offering a variety of types tailored for specific applications. Proper installation, calibration, and measurement techniques are essential to ensure accurate and reliable results. Strain gauges find applications in industries such as automotive, aerospace, energy, and research. They enable structural health monitoring, material testing, and advancements in robotics and automation. Emerging technologies, such as miniaturization and wireless integration, promise exciting prospects for strain gauge technology. Despite challenges and limitations, strain gauges provide significant benefits, including non-disruptive testing, high precision, and versatility, making them indispensable in various fields.